In recent decades, the powder coating industry has experienced growth, but the raw materials are also becoming increasingly expensive. As a result, manufacturers are forced to evaluate all aspects of their business to maintain growth and healthy profitability.
The powder coating process
The powder coating process includes several steps in which the raw materials go through different stages to form a (plastic) mix. This mix is then cooled and broken down into plastic chips before being finely ground and processed through a cyclone classifier to separate the coarse and fine particles.
Quality Control Screening
The final phase of the process involves sieving the fine powder to remove foreign contaminants such as lint. Sieving the powders at this stage ensures that only powder of the correct particle size proceeds to the filling line. This is crucial as it directly affects the quality and film thickness achievable during the coating process.
Sieving Fine Powder Coatings
Problems with traditional sieving methods and the solution
To prevent mesh clogging, some manufacturers have experimented with 'offline' sieving and rotating sieves. However, these methods can compromise product quality, as very little oversize is collected during the sieving process. Van Borselen Filters has developed the ultimate solution for this application. By utilizing Sweco round sieving machines in conjunction with ultrasonic technology, a highly efficient sieving process can be guaranteed.
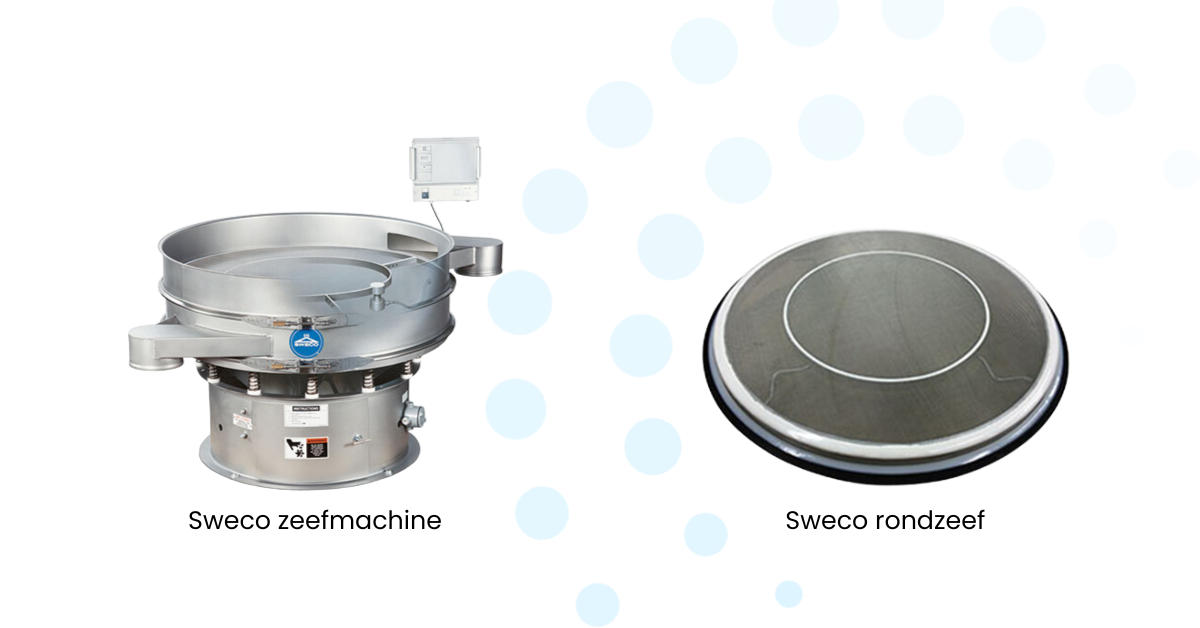
Sono-Energy sieves
The SWECO Sono-Energy™ System enables the separation of lightweight powder materials that previously seemed impossible. The Sono-Energy generates a secondary ultrasonic vibration that prevents clogging of fine meshes (60-635 meshes). There are numerous applications for epoxy powder, toner powder, and powder coatings. Sono-Energy also performs well with heavy metal powders, such as lead, nickel, and chromium, by preventing particles of nearly the same size from becoming stuck. This reduces clogging and extends the lifespan of the sieve..
Sono-Wave sieves
The Sono-Wave fully digital ultrasonic system enhances the vibration of the sieve surface through more uniform energy distribution and also offers adjustable amplitude and frequency sweep. The Sono-Wave Ultrasonic Round Vibratory Separation Equipment includes a generator available in 100W and 200W versions, which can drive two sieves simultaneously. This eliminates the need for a second generator in applications with dual decks. The ultrasonic transducer is mounted outside the sieve. With no cables or electrical components present inside the sieve, the device can meet the ATEX Zone 20 production scale, and solutions are available for any size of operation.